In modern manufacturing, CNC (Computer Numerical Control) machining technology has become the foundation of precision part manufacturing. Whether in the aerospace, medical, or automotive industries, the applications of CNC machines are ubiquitous.
These machines use computer control to achieve high-precision cutting, drilling, and polishing, and can process various materials, including metals and plastics. However, the selection of CNC machining equipment is not based on a single standard but rather determined by the complexity, geometry, and required precision of the parts. From basic 3-axis machines to high-precision 5-axis machines, each type of CNC machine tool has its unique advantages and application areas.
This article will delve into the working principles, advantages, and disadvantages of CNC machines with different numbers of axes, and how to choose the most suitable equipment based on specific needs.
Table of Contents
What is CNC Machining?
CNC (Computer Numerical Control) machining is a technology that uses computer automation to control machines for manufacturing parts, suitable for various materials such as metal, plastic, and wood.
By executing pre-written program instructions, CNC machine tools can precisely perform cutting, drilling, and polishing, enabling manufacturers to produce parts with intricate designs and high accuracy.
Advantages
- CNC machining is renowned for its exceptional precision, making it particularly suitable for industries with extremely high accuracy requirements, such as aerospace and medical.
- CNC enhances production efficiency. Through automated control, it accelerates the manufacturing process with minimal human intervention.
- The flexibility of CNC machine tools makes them applicable to a wide range of applications, providing versatility unmatched by traditional machining methods.
What are CNC Machining Axes?
In CNC machining, an axis refers to the direction in which the cutting tool or workpiece can move.
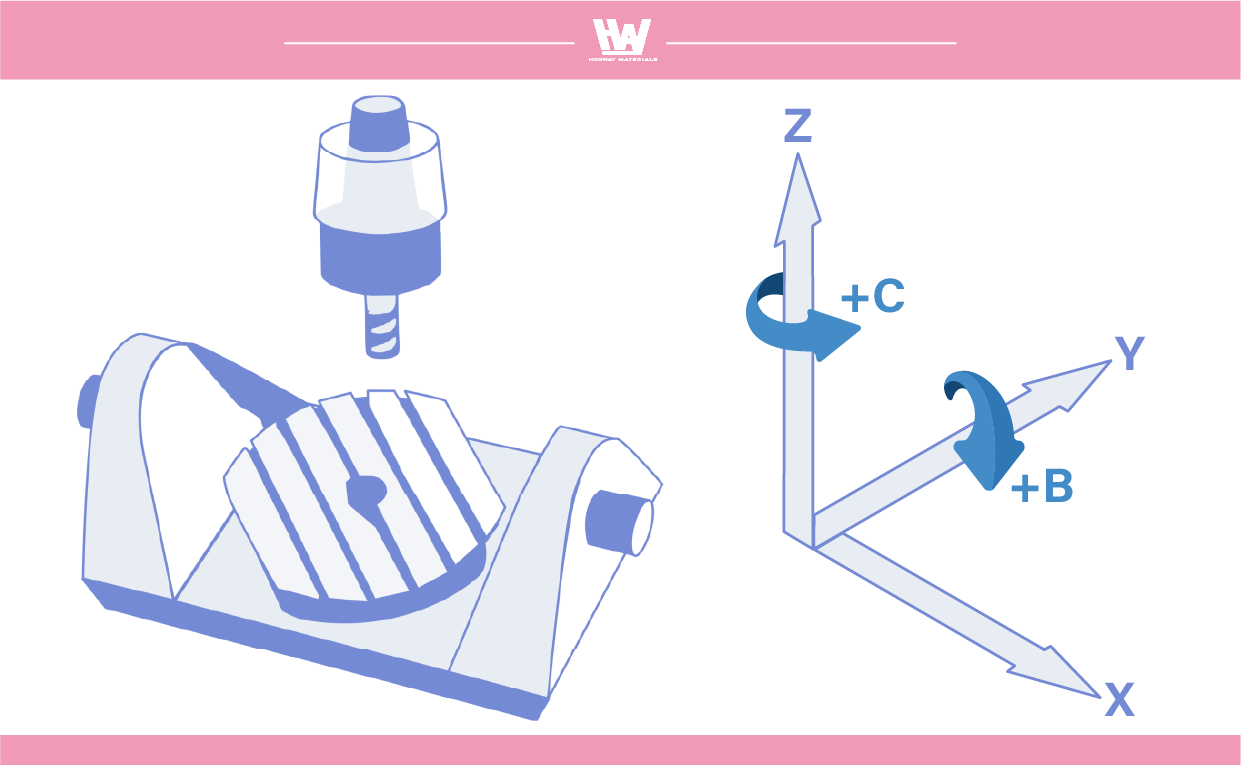
Basic Axis Motions
These axes are like the coordinates we learn in math class. Standard CNC machines typically operate along three linear axes (X, Y, and Z), allowing the tool to:
- X-axis: Move left and right
- Y-axis: Move forward and backward
- Z-axis: Move up and down
These movement directions determine how the tool precisely cuts and shapes the material.
Importance of Additional Axes
When a CNC machine adds a 4th (B) axis and a 5th (C) axis, the tool or workpiece can rotate around the X, Y, or Z axis, making machining capabilities more flexible.
This multi-axis design allows the machine to cut from different angles without frequent repositioning of the workpiece, significantly improving machining efficiency and accuracy in high-precision industries such as aerospace and medical.
3-Axis CNC
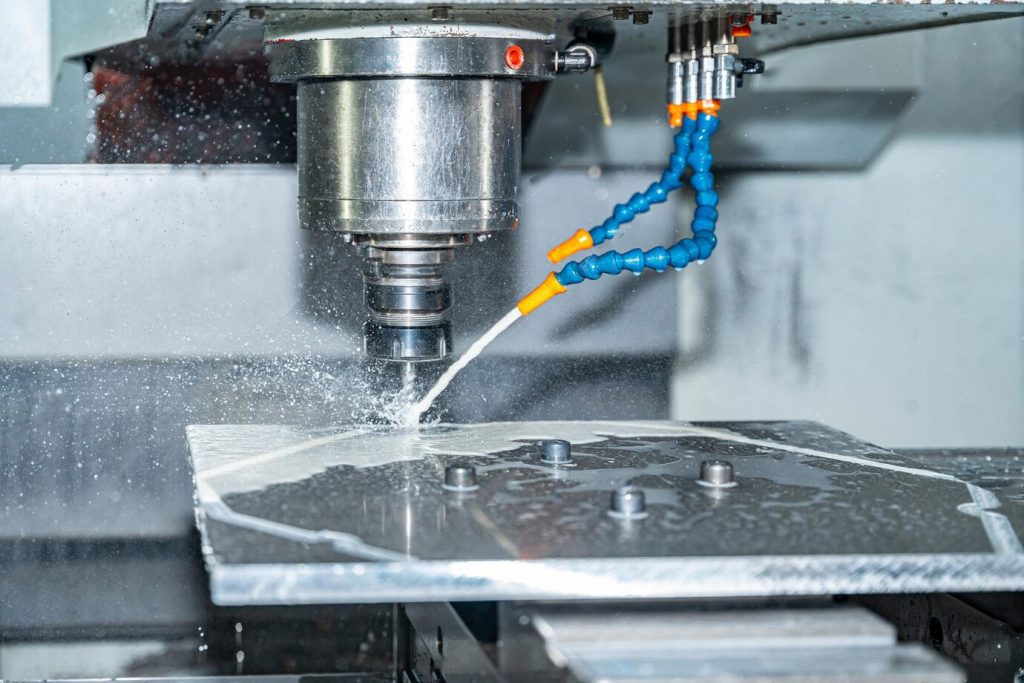
This is the most basic of the three types, moving primarily along three axes: X, Y, and Z, and does not have the rotational capabilities of 4-axis or 5-axis machines.
This configuration allows the tool to perform basic cutting and engraving on the material.
For many manufacturers, 3-axis CNC machining is ideal for producing flat parts, especially suitable for workpieces with relatively simple designs or those requiring mass production.
Advantages and Disadvantages of 3-Axis CNC
- Advantages: Cost-effective and simple to operate, particularly suitable for machining flat parts or designs with simple structures. Due to the lower initial investment and maintenance costs, these machines are well-suited for mass production, effectively reducing manufacturing costs.
- Disadvantages: Limited machining capabilities, unable to perform rotational movements. Therefore, producing complex parts requires multiple repositioning of the workpiece. This not only increases production time but also raises labor costs, making it somewhat inadequate for high-precision, multi-faceted machining needs.
4-Axis CNC
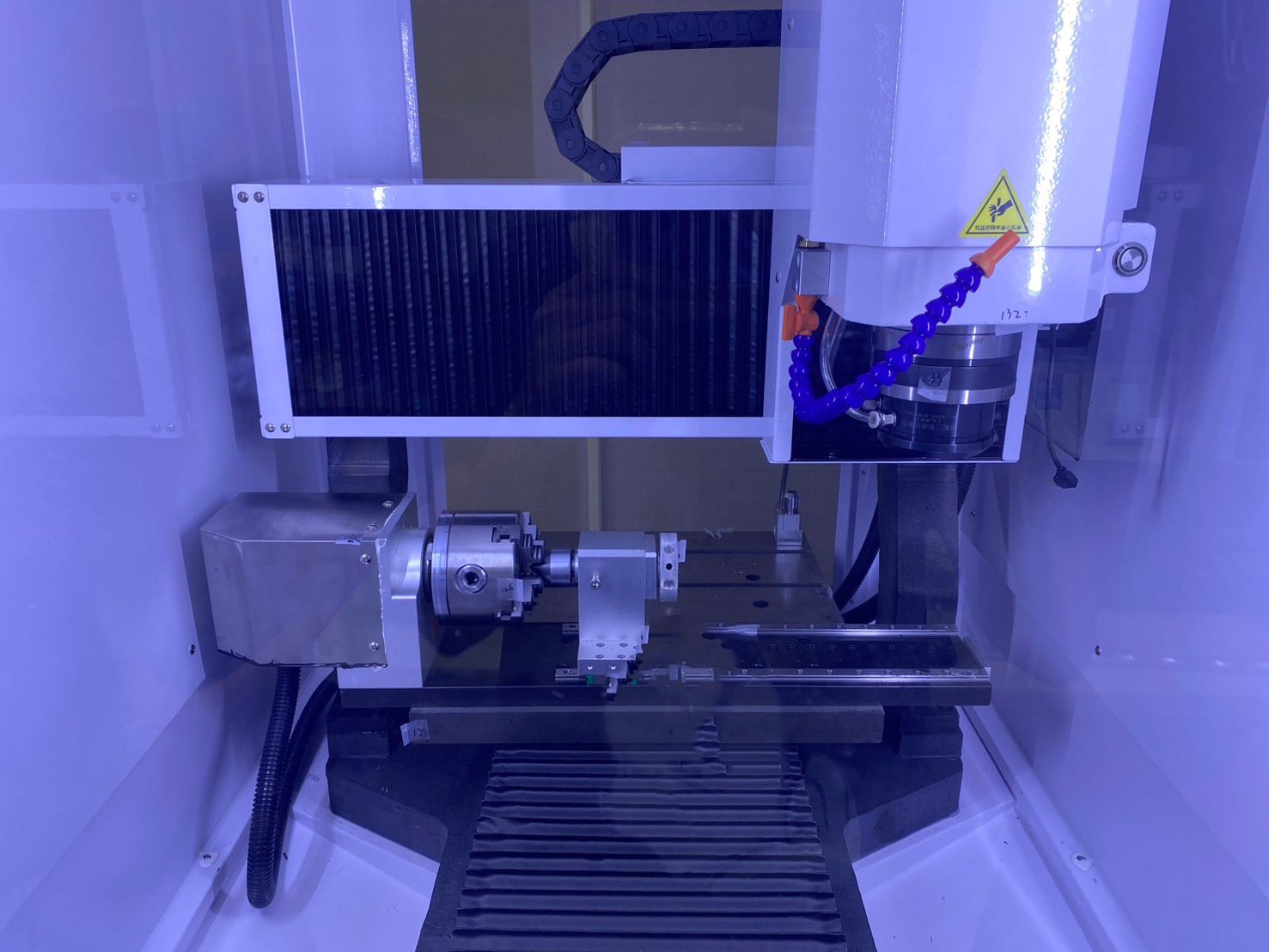
In 4-axis CNC machining, the machine tool adds a fourth axis (the B-axis), which allows the workpiece to rotate around the X-axis.
This rotational capability enhances machining flexibility, enabling the machine to produce polygonal parts and machine angled holes without frequent repositioning of the workpiece, thereby improving production efficiency and expanding design possibilities.
Features of the Fourth Axis
Through the rotational movement of the B-axis, 4-axis CNC machining allows the workpiece to rotate at different angles without manual repositioning.
This additional movement not only speeds up the machining process but also enables machining of multiple sides in a single setup, making it particularly suitable for producing cylindrical parts and angled holes, such as gears, turbine blades, and shafts.
Advantages and Disadvantages of 4-Axis CNC
- Advantages: Through the rotational movement of the fourth axis, 4-axis CNC machine tools can machine complex parts with fewer setup operations, especially suitable for multi-sided machining and the production of cylindrical parts. This not only improves accuracy but also enhances production efficiency, making it a higher-level CNC machining choice.
- Disadvantages: Although 4-axis machines are more flexible than 3-axis machines, they still have limitations in accuracy and convenience compared to 5-axis machines. Furthermore, certain complex geometries may require longer setup times and higher operator skill to complete, increasing the machining challenge
5-axis CNC
For machining requiring the highest precision and complexity, 5-axis CNC machining is the most suitable axis configuration.
This configuration includes the standard three linear axes (X, Y, Z) and adds two additional rotational axes (B-axis and C-axis). Depending on the machine type, the rotational movement can occur in the tool head or the workpiece itself, enabling precise cutting from almost any angle.
Advantages and Disadvantages of 5-Axis CNC
- Advantages: 5-axis CNC boasts exceptional accuracy and flexibility, capable of machining complex shapes and challenging geometries in a single setup. In industries highly dependent on precision, such as aerospace and medical manufacturing, 5-axis machining technology is crucial, ensuring parts meet stringent tolerances and quality standards
- Disadvantages: 5-axis CNC machines have relatively high equipment costs, and the system’s high complexity requires skilled operators with specialized technical expertise.
Applications of Different Axes
Number of Axes | 3-axis | 4-axis | 5-axis |
Motion | Three Linear Axes: X, Y, Z | Three Linear Axes: X, Y, Z + One Rotary Axis (B) | Three Linear Axes: X, Y, Z + Two Rotary Axes (B, C) |
Performance Characteristics | Cost-effective and easy to operate | Improves the accuracy, quality, and efficiency of machining freeform curved surfaces; capable of rotary machining | Can reduce the need for tools and fixtures, reducing manufacturing costs; capable of machining extremely complex curved surfaces and multiple angles, and machining multiple faces in one setup |
Applicable Workpieces | Manufacturing flat parts, drilling | Parts with rotational features, such as shafts and housings/casings | Complex curved surface parts, such as aerospace components, medical devices, precision molds |
Applicable Industries | Suitable for workpieces with relatively simple designs or requiring mass production | Automotive industry, aerospace technology, energy industry | Aerospace technology, medical equipment, scientific research and development |
3-Axis Applications
- Commonly used in electronics, automotive, and general manufacturing
- Particularly suitable for producing parts with simpler geometries, such as electronic enclosures, basic automotive parts, and flat structural components
4-Axis Applications
- Commonly used in aerospace, medical manufacturing, and energy production
- Ideal choice for manufacturing turbine blades, gears, aerospace components, and medical implants
- Capable of efficiently handling polygonal parts and precisely machining angled surfaces and cylindrical parts in a single setup
5-Axis Applications
- Commonly used in high-precision fields such as aerospace, medical, mold manufacturing, and scientific research and development
- Manufacturing complex aerospace components, custom medical implants, and intricately designed molds
How do I choose between three-axis, four-axis, and five-axis?
When choosing the number of axes, we should consider whether the workpiece has complex angles and curved surfaces. The more curved surfaces and angles, the more axes we should choose!
Part Complexity and Geometry
- For simple, flat parts or basic drilling needs, three-axis CNC machine tools are the ideal choice. These machines are simple, economical, and well-suited for handling less complex shapes.
- When machining polygonal parts, angled holes, or cylindrical shapes, four-axis CNC machine tools are a powerful choice. The added B-axis rotational capability enables the machine to machine multi-faceted features more efficiently, without additional workpiece repositioning, improving machining efficiency and flexibility.
- For highly complex parts (such as aerospace components or medical devices with curved or intricate geometries), five-axis CNC machine tools exhibit unmatched precision and versatility. With the addition of B-axis or C-axis rotational capabilities, five-axis machines can machine from multiple angles in a single setup, providing excellent results regardless of the most complex designs or high precision requirements.
Material Considerations
- 3-axis machines: Suitable for machining softer materials, such as aluminum and plastic.
- 4- and 5-axis machines: Generally more efficient when machining harder materials, such as steel or titanium.
In summary
- 3-axis machines: Ideal for basic parts with flat surfaces or simple geometries, especially when budgets are limited or ease of use is a high priority.
- 4-axis machines: Best used for parts requiring precise inclined surfaces and multi-faceted machining, particularly suitable for applications with moderate complexity, such as in the aerospace and medical industries.
- 5-axis machines: Best suited for machining parts with complex shapes and angles, commonly used in aerospace, medical, and mold manufacturing. Five-axis CNC is the best choice when the requirements are extremely high precision and minimal setup time.
Common Polishing Equipment
Ultra-fine polishing equipment>>>AS-4100 5190
- Easy-to-Use Interface
- Polishing automation
- Polishing path compensation design
- Enhance the efficiency and stability of polishing.
- Realization of free-form ultra-precision polishing head
- No polishing marks or rainbow stripes under the microscope.
- Suitable for: electroless nickel, copper, aluminum, tungsten steel and mold steel
Conclusion
Choosing the appropriate number of CNC machining axes mainly depends on the complexity of the part and material requirements. For simple flat parts or basic drilling, three-axis CNC is the most cost-effective and easy-to-operate option, suitable for softer materials such as aluminum and plastic. When multi-faceted machining, angled holes, or cylindrical shapes are required, four-axis CNC provides greater machining flexibility and precision, particularly suitable for industries such as aerospace and medical. For highly complex parts, especially those with curved or intricate geometries, five-axis CNC offers unparalleled precision and versatility, capable of machining from multiple angles in a single setup to meet high-precision requirements. Overall, as machining complexity and precision requirements increase, selecting CNC machines with more axes will enable more efficient machining, although costs and operational difficulty will also increase accordingly.
Action
- Why does grinding generate heat?>>Grinding heat
- The basic knowledge of abrasives that must be known>>>Grinding-Abrasive Introduction
- The Key Role of Grinding Wheel Performance>>Bond
- Whether the current measured surface roughness meets your expected goals>>>Comparison Chart of Grinding Polishing and Surface Roughness
- Various aspects of grinding wheel abrasive grains>>The Grinding Effect of the Grinding Wheel Particles
- What to do if the surface is deteriorated>>In-depth analysis of grinding to avoid surface deterioration
- The surface is not rough, the light is not smooth>>What is surface roughness?
- Different grinding states of cutting edge>>In-depth understanding of grinding wheel cutting edge shapes, variations, and self-sharpening mechanisms
- Action>>>Diamond and CBN grinding wheel, Polishing abrasive, Polishing Equipment, Polishing Tools
- Review
We offer customized adjustments to the grinding process, tailored to meet processing requirements for maximum efficiency.
After reading the content, if you still don’t know how to select the most suitable option,
Feel free to contact us and we will have specialist available to answer your questions.
If you need customized quotations, you’re also welcome to contact us.
Customer Service Hours: Monday to Friday 09:00~18:00 (GMT+8)
Phone: +8867 223 1058
If you have a subject that you want to know or a phone call that is not clear, you are welcome to send a private message to Facebook~~
Honway Facebook: https://www.facebook.com/honwaygroup
You may be interested in…
- Meta Polishing
- Several Methods for Achieving Mirror Finishing
- The Key Role of Grinding Wheel Performance – Bond
- Shining In the Fields of Optics and Medicine ── Europium
- How to Expend the Lifespan of a Grinding Wheel? Grinding Conditions and Wear Calculations
- The Physical Basis and Applications of Nanodiamonds